In the automotive industry, precision and durability are critical, especially when it comes to components like crankshafts. Cubic Boron Nitride (CBN) grinding wheels have become an essential tool in the finishing process of crankshafts, offering unparalleled performance and efficiency.
Advantages of CBN Grinding Wheels
CBN grinding wheels are known for their hardness, second only to diamond, making them ideal for machining hard materials such as steel and cast iron. The use of CBN wheels in crankshaft finishing provides several benefits:
High Precision and Surface Quality: CBN wheels deliver a smooth and precise finish on crankshaft journals, which is crucial for ensuring efficient engine operation.
Long Tool Life: These wheels require less frequent dressing compared to conventional grinding wheels, which significantly reduces downtime and increases productivity.
Reduced Grinding Burns: CBN wheels minimize the risk of thermal damage and grinding burns on crankshafts, thereby enhancing the fatigue strength and longevity of the components.
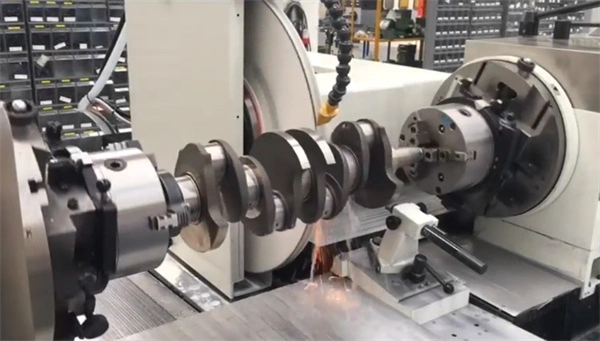
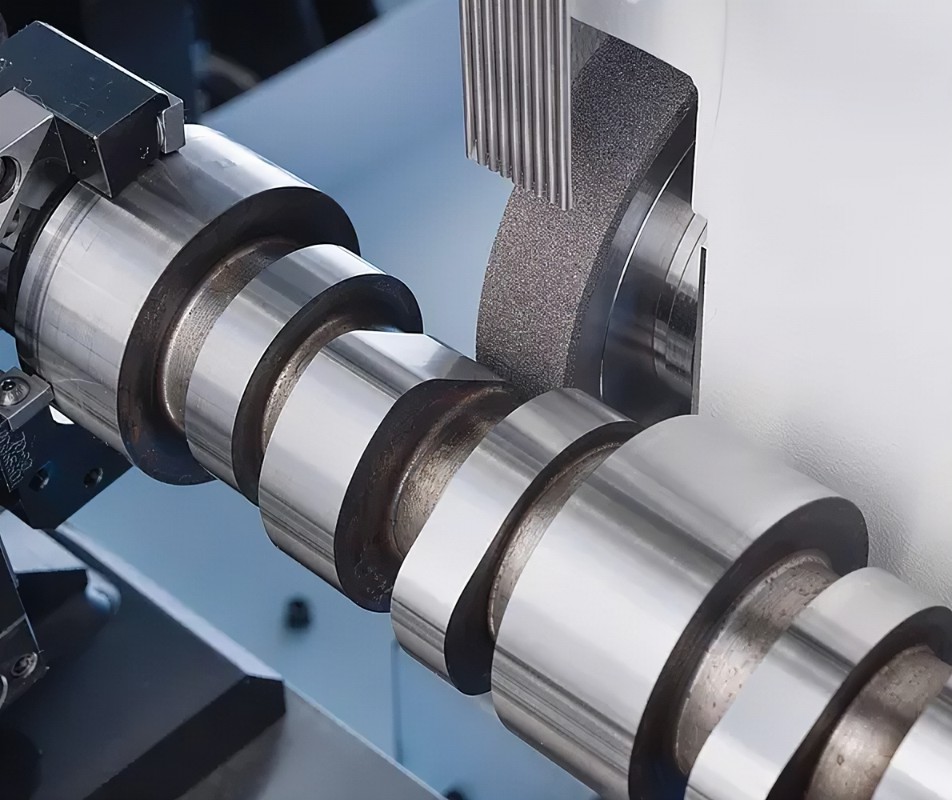
Application in Crankshaft Manufacturing
CBN grinding wheels are particularly effective in high-speed and high-precision applications. They are extensively used in the automotive industry for grinding crankshaft main bearings and pin bearings, where maintaining tight tolerances and achieving a flawless surface finish are critical. The vitrified bond CBN wheels are especially suited for high-efficiency grinding processes, which are essential for mass production environments.
Materials and Compatibility
CBN grinding wheels are versatile and can be used on various materials, including different types of steel and cast iron. Their compatibility with advanced CNC grinding machines makes them suitable for a range of crankshaft grinding tasks, from rough grinding to finishing.
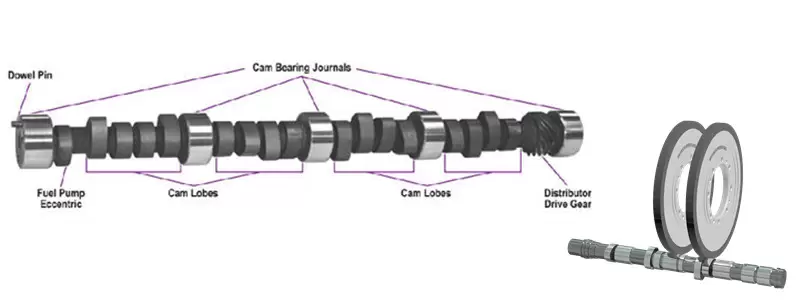
In summary, CBN grinding wheels play a crucial role in enhancing the quality and efficiency of crankshaft manufacturing in the automotive industry. Their ability to deliver high precision, reduce thermal damage, and extend tool life makes them indispensable for modern crankshaft finishing processes.
Post time: Aug-09-2024