When it comes to achieving high precision in machining, both honing and internal grinding are essential processes. Understanding the differences between these techniques can help you choose the right method for your specific needs. Here’s a detailed comparison of honing and internal grinding based on their characteristics, advantages, and typical applications.
Honing: Precision and Surface Quality
Honing is primarily used to enhance the surface finish, roundness, and dimensional accuracy of a part. It involves a rotating and reciprocating motion of abrasive stones or diamond hones within a bore. This process is known for its ability to produce a smoother and more precise surface without significant material removal.
Key Characteristics of Honing:
Surface Finish: Honing achieves a high-quality surface with a crosshatched pattern, beneficial for oil retention and wear resistance.
Precision: This process can improve the shape accuracy of the workpiece, with cylindricity and roundness often within 0.001 mm. It's ideal for small to medium-sized through holes and parts with uneven wall thickness.
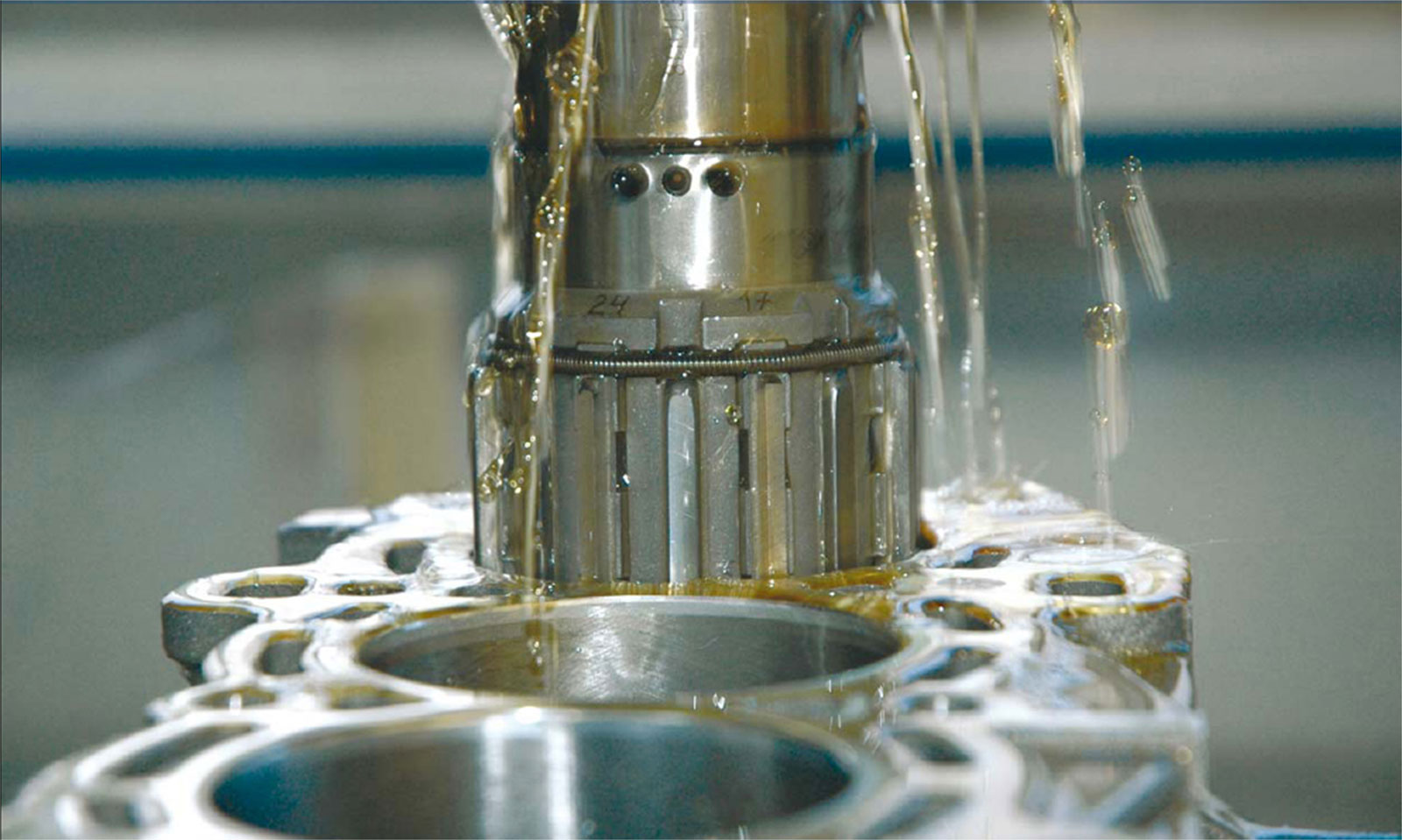
Applications: Honing is widely used for finishing engine cylinder bores, hydraulic cylinders, and gears, where high-quality internal surface finish and precise dimensions are crucial.
Internal Grinding: Material Removal and Accuracy
Internal grinding is a more aggressive material removal process. It uses a rotating grinding wheel to shape the internal surfaces of a workpiece, making it suitable for tasks requiring significant material removal and high dimensional accuracy.
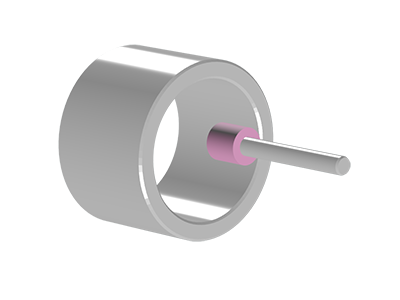
Key Characteristics of Internal Grinding:
Material Removal: This process removes larger amounts of material quickly, making it ideal for shaping and stock removal.
Surface Finish: While it can achieve high levels of surface finish, the results can vary from rough to smooth depending on the specific grinding process used.
Types of Internal Grinding:
Center Internal Grinding: Suitable for parts like sleeves, gears, and flanges, where the workpiece rotates around the spindle.
Planetary Internal Grinding: The grinding wheel rotates and also moves around the center of the hole, used for large, non-rotating parts.
Centerless Internal Grinding: The workpiece is supported and driven by a guide wheel, used for cylindrical parts
Applications: Internal grinding is used for tasks requiring high dimensional accuracy, such as finishing the inner holes of sleeves, gears, and flanges. It's also effective for parts that need intricate profiles and contours.
Choosing Between Honing and Internal Grinding
The choice between honing and internal grinding depends on the specific requirements of your part:
For high precision and superior surface finish: Honing is the preferred method, especially for parts requiring excellent geometric form and minimal material removal.
For significant material removal and complex profiles: Internal grinding is more suitable, providing the necessary accuracy and efficiency for shaping and stock removal tasks.
By understanding the strengths and applications of each process, you can select the most appropriate method for achieving your machining goals. Whether it's the fine surface finish of honing or the robust material removal capability of internal grinding, each process plays a critical role in precision manufacturing.
Post time: Jun-21-2024